
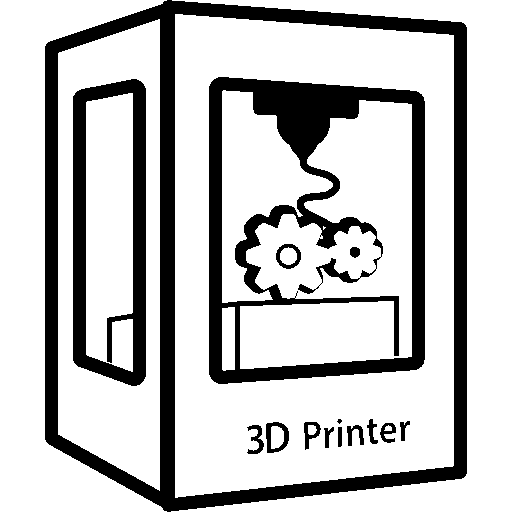
FreeCAD has improved drastically with the 1.0 update. There’s no need to tolerate this corporate BS.
FreeCAD has improved drastically with the 1.0 update. There’s no need to tolerate this corporate BS.
Isn’t wind energy better on balconies?
I have different subfolders per project for it’s components.
Project/KiCAD
Project/FreeCAD/Model1
Project/FreeCAD/Model2
Etc.
Each project has it’s own set so it’s easy to find. I think it’s better than having all 3D printing related things together and then having to sort which project it belongs to.
Officer: Why were you speeding?
Me: Wanted to avoid ads.
Less chaotic huh? Geez.
That meme was prophetic.
Samsung phones had this for years but only in specific regions. I live in the Netherlands and have changed my phone’s CSC to Vietnam just to unlock call recording. It works natively in the dialer since Android 10 or older. I had it with the Note 9.
You’re surprised at the large concentration of nerds here?
OBEY
CONSUME
If it’s PLA or PETG it’s probably still usable. PLA can get brittle if it’s wet though but drying should make it usable again.
I use a cheap food dehydrator to dry filament.
Well. I’m not sure I fully understand it. The way I calibrated e steps was to tell it to extrude 100mm of filament and then measures how much filament was pushed through the nozzle. This resulted in a value of about 680 steps/mm.
This always overextrudes and setting it down to 640 steps/mm made it much better.
Setting flow rate in the slicer does not seem to have the same effect.
Lowering e-steps gave the result I wanted but with a lower value than was calibrated for.
Sounds good. I’ll definitely give those a try to further calibrate it.
I have the issue that the nozzle hits infill during travel motions and it probably has to do with minor overextrusion.
Hmm. I bought it a few years ago when there weren’t many all metal hotends. It’s never caused any issues.
Back then it cost me about 80 euros which was a bit steep but acceptable.
Back then my reasoning was that I didn’t want any PTFE close to the hotend, fearing offgassing and limiting my options for filament types.
Detail. I’m looking to achieve tighter tolerances with 3D printing, going for dimensional accuracy.
It has gotten more difficult. I remember windows 7 being just clicking Next until it was done. Win10 requires a signup, clicking no on several telemetry pages with dark patterns, a whole bunch of BS “features”.
I’d say that is above windows. R-ing the FM is quite essential to arch or gentoo.
That doesn’t really matter too much and is mostly personal preference.
The biggest difference is which package manager and how up to date each program in there is. Arch and OpenSuse Tumbleweed will have quite up to date packages as they’re rolling release models while Mint and Ubuntu tend to be a bit slower and more stable.
I suggest going through the installation process of Arch linux at least once because it does teach you the basics of Linux but for usability you’d be better off with a distro that has a GUI installer.
Can’t you get like, a diamond drill bit and just give it a light tap? Tempered glass breaks easily if the outside layer is compromised.